
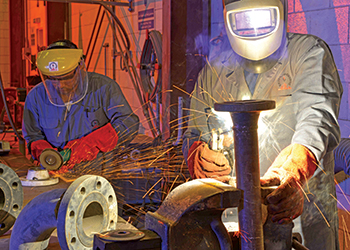
For the first time Banagas received the International Sector Award which demonstrates the company’s best health and safety management performance within the oil and gas industry in the region
Banagas continues to be internationally recognised for its world class standards of occupational safety. During the year 2015, the company at a ceremony held in London, was presented with the Oil and Gas Sector’s Award & International Sector Award by the Royal Society for the Prevention of Accidents (ROSPA).
For the first time Banagas received the International Sector Award which demonstrates the company’s best health and safety management performance within the oil and gas industry in the region. The ceremony was attended by Dr Shaikh Mohamed bin Khalifa Al Khalifa, chief executive, and Khalid Ahmed, general manager – production.
Banagas also received the International Safety Award from the British Safety Council (BSC), and took second place in the Gas Processors Association (GPA) of the US Division II International Category. These latest awards are an addition to previous accomplishments and awards acquired by the company.
Dr Shaikh Mohamed says: "These significant international awards are the result of the commitment on the part of all employees to adhering to safety rules and regulations and their full awareness and understanding of their occupational responsibilities. A heightened sense of safety exists all the time within Banagas based on a well-conceived methodology using international standards developed by international safety bodies such as the GPA, the Royal Society for the Prevention of Accidents and the US National Safety Council. The fact that Banagas has received prestigious awards from such organisations is indicative of our full time commitment to the highest standards of occupational safety."
Dr Shaikh Mohamed praises the role of the Board of Directors of the Company in supporting any programme that aims to further promote Banagas at international level.
"The company’s goal is to continue maintaining such excellence," Dr Shaikh Mohamed says. "I would like to express our total confidence that the constant awareness of our employees and their uncompromising determination to apply safety rules and regulations in their work will achieve this goal. We will continue to develop and improve employment conditions and promote safety throughout the company," the chief executive states, "wishing all employees every success in attaining mutually desired objectives," he adds.
International Safety Award
At a ceremony held in London, attended by Dr Shaikh Mohamed and Khalid Ahmed, general manager-production, the company was presented with the "International Safety Award with Merit" from the British Safety Council in recognition of the company’s commitment to keeping its employees and workplaces healthy and safe during 2014.
To mark this occasion, Dr Shaikh Mohamed said: "This major achievement has come as a result of the commitment on the part of all employees to adhering to safety rules and regulations and their full awareness and understanding of their occupational responsibility. This sense of safety exists all the time within Banagas. A well-conceived methodology has been adopted, based on international standards developed by specialised safety authorities such as the Royal Society for the Prevention of Accidents (ROSPA), the Gas Processors Association (GPA) of the US and the US National Safety Council. The fact that Banagas has won several international awards from such Internationally recognised organisations is indicative of our full commitment to the highest standards of occupational safety."
He praised the significant role of the Board of Directors of the company in supporting any programme that aims at further promoting Banagas and positioning it at highest international levels.
"The company’s goal is to continue maintaining such excellence," Dr Shaikh Mohamed adds. "I would like to express our full confidence that the constant awareness of employees and their uncompromising determination to apply safety rules and regulations in their work will achieve this goal. The company will continue to develop and improve employment conditions and to promote safety within all our facilities," he states.
Lynda Armstrong OBE, chairperson of the Trustees of the British Safety Council, congratulated the company on their success in winning this Award: "The British Safety Council commends Bahrain National Gas Company on their achievement. She adds that "the award is in recognition of their commitment and effort to keep their employees and workplaces free of injury and ill health. Our warmest congratulations."
International Business Awards
Banagas also won five International Business Awards including the Gold award for the Executive of the Year. These International Business Awards, known as the "Stevie Awards", recognise the positive contribution of successful companies and business people worldwide.
Companies and individual winners are selected every year by a committee made up of more than 250 judges from all over the world.
In 2015, organisations from more than 50 countries competed for these awards. Banagas was honoured to receive the following awards:
• Gold Award – Executive of the Year – Energy Sector – Dr Sheikh Mohammed Bin Khalifa Al-Khalifa;
• Gold Award – People Choice Award for Favourite Company;
• Gold Award – Banagas – As Advocator of environment, health and safety practices – Health and Safety and the Environmental Programme of the Year in the Middle East and Africa;
• Gold Award – Company of the Year – Energy Sector; and
• Gold Award – Banagas’ Debottlenecking – Energy Industry Innovation of the Year.
On this occasion, Dr Shaikh Mohamed expressed his deep pride and appreciation for Banagas receiving these honours. "We are immensely proud of this achievement. Our success in receiving the "International Stevie Awards’ is the result of the outstanding performance of all Banagas employees. I take this opportunity to thank all employees of the company for their dedication and loyalty which has enabled us to achieve such outstanding success."
She policy
The board of directors of Banagas considers the occupational safety and health of its employees and the protection of the environment as one of their primary responsibilities. The company says it is committed to providing a safe and healthy work place for all employees and contractors working within the facilities and shall take all measures and precautions to minimise and prevent personal accidents, pollution, damage to property and the environment.
To fulfil this commitment, the company shall provide the necessary resources to:
• Comply with occupational safety, health and environment rules and legislation enacted in Bahrain and to other requirements to which the company subscribes, and maintain communication channels with the concerned authorities;
• Develop and maintain guidelines and clearly defined procedures on occupational safety, health and protection of the environment systems;
• Provide appropriate occupational safety, health and environmental awareness and training to enable management, employees and contractors to meet their respective responsibilities; and
• Monitor, continually improve and evaluate performance of the systems to ensure that high standards are maintained.
She initiatives
Management of gaseous air pollution: In compliance with Ministerial Order No 3 for 2001, issued by the Ministry of State for Municipalities and Environment, gas emissions produced by gas turbines and gas dehydration units at compression stations and the main plant are regularly measured and reported to the Public Commission for the Protection of Marine Resources, Environment and Wildlife.
Elimination of ozone depleting gases: Banagas was the first company in Bahrain to eliminate the use of halons in firefighting systems, replacing them with more environmental friendly ozone-protective products, pursuant to the resolutions of the Montreal Protocol to which Bahrain is signatory.
Dedicated landfill for industrial waste: A dedicated landfill has been designated for disposal of hazardous industrial waste such as filters and carbon substances used in cleaning hydrocarbons from impurities. Procedures have also been developed for waste management and transportation to the industrial waste landfill designated by the Public Commission for the Protection of Marine Resources, Environmental and Wildlife.
Elimination of items containing asbestos: A specialised committee has identified all spare parts containing asbestos and replaced them with environment-friendly substitutes.
Forestation of the Sakhir area: In support of the national environmental protection campaign 2,000 trees have been planted in the Sakhir Area near the company’s facilities.
Noise level controls: Noise is created by turbines, compressors, air-cooler fans and pumps. High noise areas have been identified as those where the intensity of sound reaches 85+ dB.
Noise levels in the work areas have been reduced by using silencer partitions while high level noise worksites have been provided with signs indicating the need to use ear protection.
Hazop study: The company has developed a Hazard and Operability (Hazop) procedure for all engineering modifications which involves the application of a formal, systematic and rigorous examination to identify hazards and assess their consequences and risks to personnel and equipment. A Hazop committee is assigned to examine the process on the principle that a team approach to hazard analysis will identify more problems than individuals working separately.
Management of Change (MOC): A MOC procedure has been developed to systematically manage changes in process, technology, equipment, facilities or procedures (including chemicals and control system). MOC review meetings are conducted on a regular basis by a technical team comprising members identified by change owner and the actioning department manager.
Risk Based Inspection (RBI): A risk-based approach to inspection has been implemented by the company to identify the likelihood of failure and its consequences. RBI methodology is used to prioritise inspection, usually by means of non-destructive testing. Those with high probability and high consequence are given higher priority for inspection than those that are high probability but for which failure has low consequences. This strategy allows for rational investment of inspection resources.
Implementation of international standards: Banagas adapted OHSAS 18001 Standard, an internationally accepted standard on occupational health and safety management systems and ISO 14001, an internationally accepted standard on its environmental management system to develop its integrated safety, health and environmental (SHE) management system. Banagas has been awarded certification for both standards.